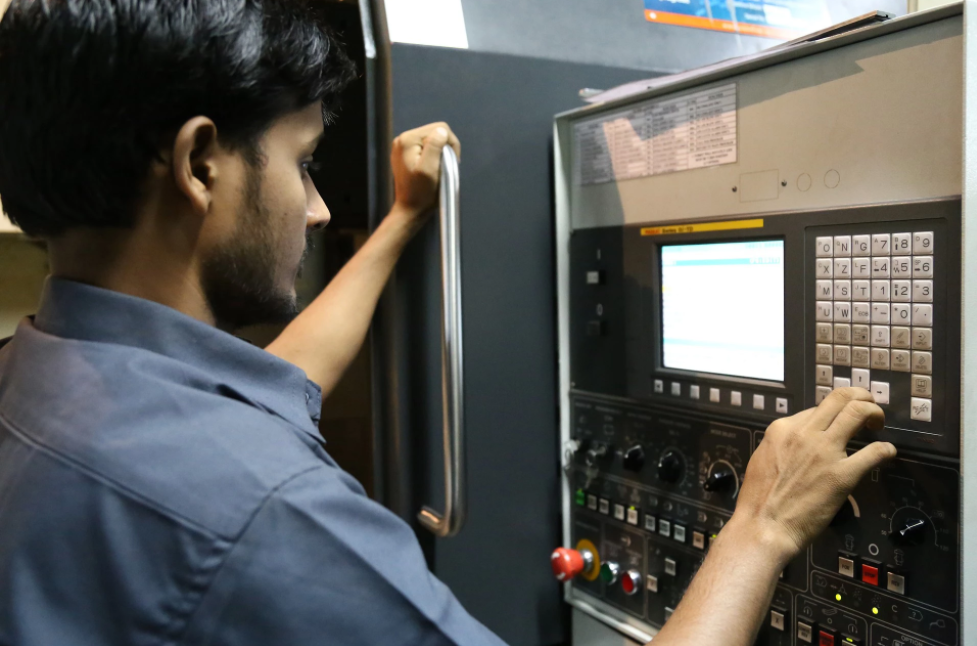
A manutenção de um sistema de refrigeração é essencial para uma instalação farmacêutica, pois deve garantir a confiabilidade do sistema por um baixo custo. A proposta deste trabalho é alcançar aumento de disponibilidade e redução do custo de manutenção para peças utilizadas em um sistema de chillers de uma indústria farmacêutica. Durante este trabalho foi definida uma metodologia de trabalho, na qual houve o levantamento de dados seguido da elaboração de um plano de ação e posterior análise dos resultados obtidos. A coleta dos dados foi feita por meio dos dados históricos no sistema de controle de manutenção e entrevistas com operadores e técnicos de manutenção responsáveis pelos equipamentos em questão. Posteriormente foram propostas ações para alcançar os objetivos traçados, nas quais foram implantadas melhorias em três linhas de trabalho: análise de falhas históricas em busca do aumento de disponibilidade dos equipamentos, a revisão dos planos de manutenção e a redução de custo em peças de manutenção. Por meio da aplicação das ações propostas, foi alcançado um aumento substancial da disponibilidade dos equipamentos, redução de custo de R$ 800.000,00 a cada 10 anos, para a troca de gaxetas dos trocadores de calor, e a redução de 76% do número de intervenções anuais nos equipamentos com a revisão dos planos de manutenção. Assim conclui-se que os objetivos foram alcançados com êxito e sistema de chillers se tornou mais confiável. PALAVRAS-CHAVE: Chiller. Disponibilidade. Custo. Manutenção.
- INTRODUÇÃO
A manutenção dos equipamentos de uma instalação industrial durante décadas foi considerada como um mal necessário, pois a mentalidade de manutenção em ambientes fabris era constituída apenas por conceitos ligados a manutenção corretiva. Com o passar do tempo houve uma mudança no foco da manutenção industrial quando se passou a tentar evitar as paradas de equipamentos por falha de seus componentes, e assim foram se tornando mais usuais formas de manutenção como a preventiva, inspeção e preditiva. (XENOS, 1988) O sistema em estudo faz parte do departamento de utilidades de uma indústria farmacêutica que possui quatro Chillers que resfriam água até 6°C. São necessários ao menos dois equipamentos para atender a demanda da fábrica. O fluido resfriado é recalcado por seis bombas centrifugas até os pontos de utilização dessa água, ou seja, os sistemas de Aquecimento, Ventilação e Ar Condicionado, (Heating, Ventilation, and Air Conditioning – HVAC) da fábrica e para o processo de envase do medicamento. Após a troca térmica realizada nos equipamentos clientes, o fluido é conduzido novamente aos chillers por quatro bombas centrifugas, formando assim um sistema fechado. 3 Chillers com sistemas de compressão de gases refrigerantes são comumente utilizados em indústrias petroquímicas, farmacêuticas e geração de energia. São equipamentos que possuem alta durabilidade e baixo custo de manutenção e operação. (TRANE, 2014; YORK, 2015) Segundo Alves (2016), chillers são equipamentos de um sistema de refrigeração de ar responsáveis pela retirada de calor da água por meio de expansão de um gás refrigerante comprimido, o sistema é composto por quatro peças principais o compressor, o condensador, o evaporador e o dispositivo de expansão.
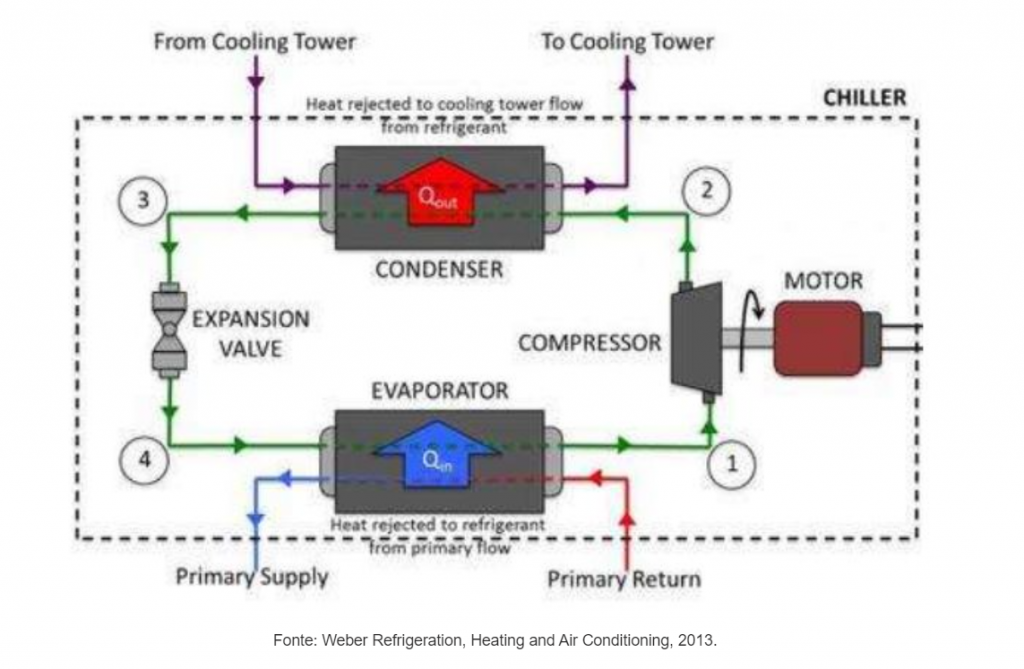
O sistema em questão possui quatro chillers que podem ser representados pelo esquema simplificado exposto na Figura 1. O funcionamento do mesmo se inicia pela compressão do fluido refrigerante pelo compressor parafuso que é movido por um motor de seiscentos cavalos. O Fluido comprimido a alta temperatura em forma de gás é conduzido a um trocador de calor de placas de escoamento contracorrente, no qual realiza a troca de calor com a água resfriada por um sistema de torres de resfriamento. O mesmo perde energia térmica e condensa. Após passar pelo condensador o fluido refrigerante é conduzido para a válvula de expansão onde sofre uma grande variação de volume que causa uma redução brusca de 4 temperatura. O fluido refrigerante expandido que se encontra a baixa temperatura troca calor com a água no evaporador, em um trocador de calor de placas de escoamento contracorrente. Neste momento do fluido refrigerante se encontra em estado gasoso para ser admitido pelo compressor e fechar o ciclo. Segundo Incropera e DeWitt (2008), existem diversas configurações para trocadores de calor, no entanto os que possuem escoamento contracorrente são os mais eficientes, devido o diferencial de temperatura, entre os fluidos quente e frio, permanecer elevado em todo o trocador de calor. Os equipamentos nos quais o projeto teve seu foco estão em operação a cerca de 10 anos. Percebeu-se que os mesmos estavam apresentando uma variação de disponibilidade muito grande, o que foi constatado como uma mudança de comportamento no que tange as suas falhas. Esse fato foi notado estatisticamente, e apresentado no Gráfico 1. É possível notar que o sistema não apresentava uma tendência em relação ao número de defeitos e falhas a partir de 2014 e um aumento de indisponibilidade dos equipamentos incentinvando assim o inicio do projeto.
Gráfico 1 – Relação de tempo de indisponibilidade e quantidade de defeitos/falhas detectados no sistema
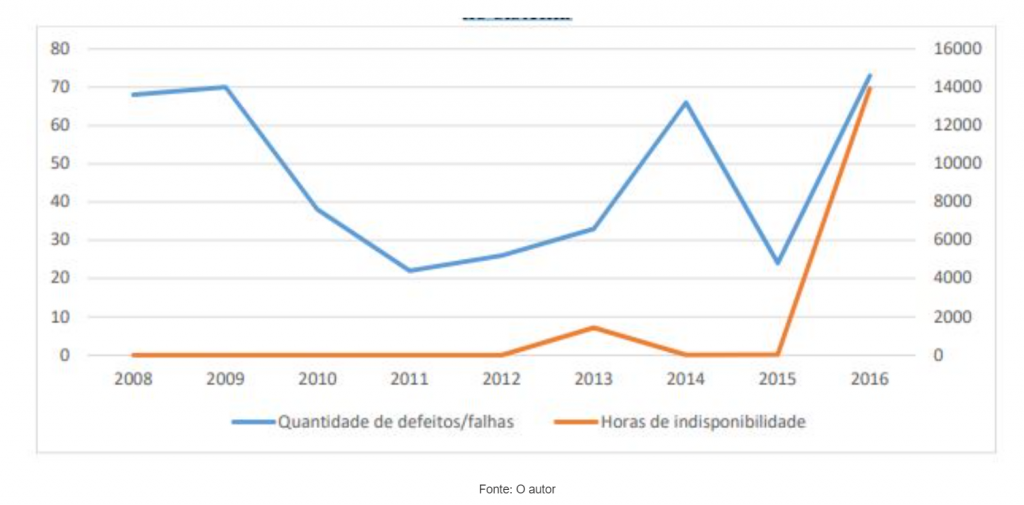
A indisponibilidade apresentada no gráfico é referente aos quatro chillers do sistema durante cada ano de operação. Este dado não é consistente antes de 2013, pois o mesmo não estava disponível no sistema de gerenciamento de manutenção. O gerenciamento da manutenção no contexto em que estes equipamentos estão inseridos é feito por um sistema ERP (Enterprise Resource Planning ou Sistema Integrado de Gestão Empresarial) da empresa SAP (Software Applications and Products ou aplicativos de software e produtos) e orientada por um procedimento interno da empresa que estabelece que 0 2000 4000 6000 8000 10000 12000 14000 16000 0 10 20 30 40 50 60 70 80 2008 2009 2010 2011 2012 2013 2014 2015 2016 Quantidade de defeitos/falhas Horas de indisponibilidade 5 todo plano de manutenção deve ser revisado periodicamente. Esta orientação do procedimento garante que os planos estejam atualizados e assim condizentes com a situação mais atual do equipamento. O procedimento interno da empresa segrega as ocorrências nos equipamentos dentro do sistema ERP pelo tipo de notificação gerada, sendo as opções M1 e M2 que caracterizam defeitos e falhas respectivamente. Segundo Fabro et. al (2003), a manutenção de uma instalação industrial se tornou uma emergente alternativa de aumento da competitividade das empresas, pois as atividades de manutenção têm impacto direto nos custos, disponibilidade e operação da instalação. O novo objetivo principal do setor de manutenção é aumentar a confiabilidade dos processos, diminuindo os riscos de interrupções de funcionamento e indisponibilidades por falhas. Os termos falha e defeito foram definidos na NBR 5462 (ABNT, 1993) como o não atendimento de um sistema ou componente às funções requeridas para o mesmo e o desvio da função requerida de um componente ou sistema em operação, respectivamente. A mesma norma define ainda que a função requerida é o que é esperado que o componente realize dentro do sistema onde está inserido. Pode-se entender de forma mais clara estes conceitos na definição de Kardec; Nascif (2001), que explicita defeito como sendo a diminuição de rendimento do equipamento, e a falha como uma incapacidade de satisfazer um padrão de funcionamento previamente definido. O presente trabalho retrata o processo de reformulação das atividades de execução e controle das manutenções realizadas em um sistema de resfriamento de água devido a uma crescente indisponibilidade dos equipamentos em estudo. Assim, os objetivos deste trabalho foram: Aumentar a disponibilidade dos equipamentos; reduzir intervenções nos equipamentos para manutenções periódicas; reduzir custo de manutenção. MATERIAIS E MÉTODOS A metodologia utilizada para a confecção deste trabalho foi documental. Por meio da análise dos problemas, foram identificadas oportunidades de melhoria para o sistema e fazendo assim necessário a execução de um estudo que envolvesse uma análise histórica dos dados de manutenção e confecção de um plano de ação, buscando assim alcançar os objetivos definidos. 6 Observando a crescente indisponibilidade de equipamentos no sistema de resfriamento de água, os dados coletados do sistema de gerenciamento de manutenção nortearam os trabalhos, indicando os pontos de maior recorrência de intervenções e que causaram a elevação do índice de indisponibilidade. Desta análise foram propostas ações para reduzir a indisponibilidade apresentada pelo sistema. Também foram revistos os planos de manutenção do sistema considerando histórico de falha dos equipamentos e orientações do fabricante, assim abrangendo as peculiaridades de cada equipamento e o que é indicado pelo fabricante, e contemplando mudanças de periodicidade de atividades preventivas e implementação de novas preditivas e inspeções no sistema. Por fim foi analisado o custo de peças de manutenção por meio de dados retirados do sistema de controle de manutenção. Foram propostos e implementadas ações para a redução de custo relacionado a peças utilizadas nos equipamentos.
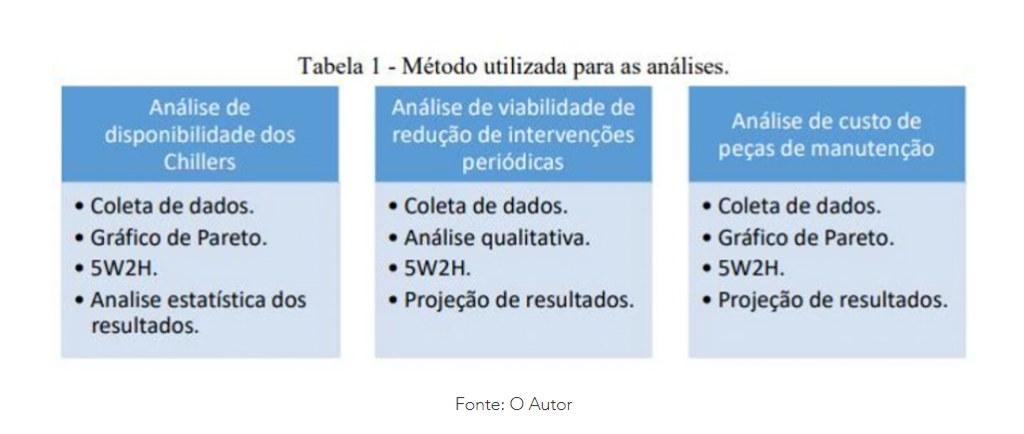
Para a análise e tabulação dos dados de manutenção colhidos do SAP, foi utilizado o software Microsoft Excel para uma melhor organização e disposição dos mesmos, de forma clara e sucinta. Os dados colhidos foram variaram com a análise que seria feita, sendo estes dados posteriores a 2008 para todas as análises. Estes dados serviram de embasamento para as modificações implementadas durante o projeto. As ações propostas foram finalizadas em dezembro de 2016, e os dados existentes em 2017 foram considerados como resultados das ações propostas. Para as ações que ainda não possuem dados para comprovação de sua efetividade, foi feita uma projeção para análise dos prováveis resultados. Análise de disponibilidade dos Chillers • Coleta de dados. • Gráfico de Pareto. • 5W2H. • Analise estatística dos resultados. Análise de viabilidade de redução de intervenções periódicas • Coleta de dados. • Análise qualitativa. • 5W2H. • Projeção de resultados. Análise de custo de peças de manutenção • Coleta de dados. • Gráfico de Pareto. • 5W2H. • Projeção de resultados. 7 RESULTADOS E DISCUSSÃO Análise de falhas históricas em busca do aumento da disponibilidade Segundo Takata et. al (2004), realizar uma intervenção para correção quando o defeito ainda não se tornou uma falha, reduz o tempo de indisponibilidade do equipamento. Visando diminuir a indisponibilidade dos equipamentos foi gerado um Pareto para que pudesse ser avaliado os maiores causadores de indisponibilidades para o sistema, pontos que podem ser notados no Gráfico 2. A indisponibilidade do sistema em sua maior parte é causada por vibração dos motores de acionamento dos chillers, desgaste dos selos mecânicos e fim de vida útil das gaxetas dos trocadores de calor. Assim a equipe foi levada a encontrar formas de evitar que os equipamentos ficassem indisponíveis devido estes fatores.
Gráfico 2 – Pareto de causas de indisponibilidade do sistema.
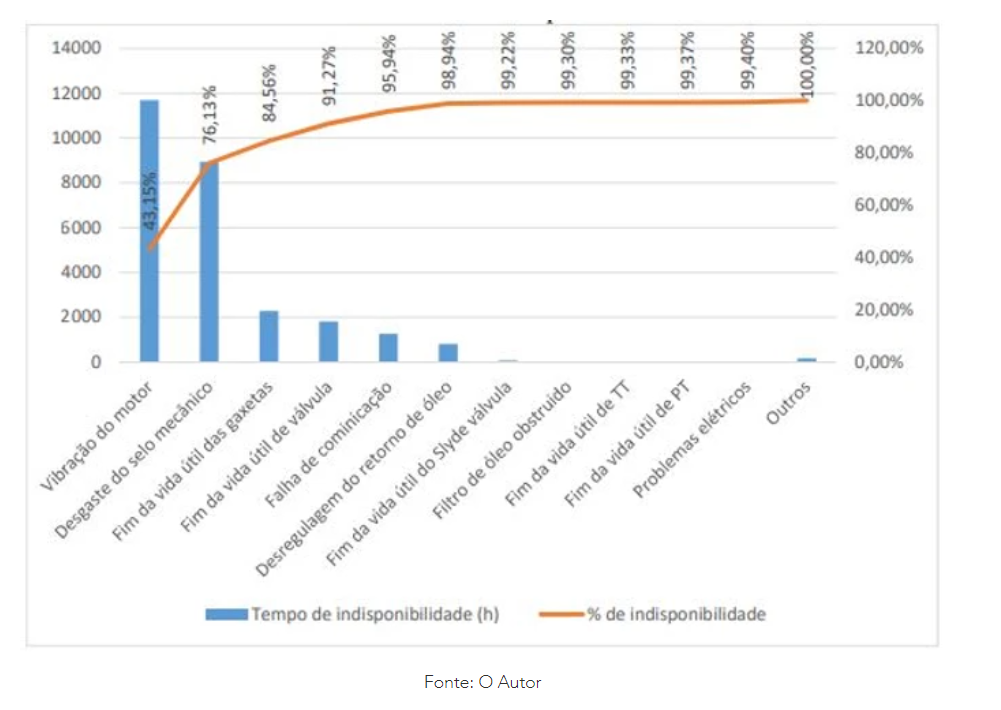
O primeiro ponto de indisponibilidade analisado foi o desgaste dos selos mecânicos. Durante a análise foi identificado que o desgaste ocorreu devido a uma condição inerente ao funcionamento dos selos mecânicos. No entanto o selo mecânico utilizado é o indicado para o equipamento como foi informado pelo fabricante do equipamento em seu manual de operação e manutenção.
Dois pontos foram identificados como os responsáveis pelo índice, a indisponibilidade de selos em estoque, devido ponto de reposição do estoque abaixo do necessário, e a falta de acompanhamento do desgaste da peça. Visando o aumento da confiabilidade do sistema e redução da indisponibilidade dos chillers devido falta de selos mecânicos em estoque, foi realizado o aumento do estoque para que não houvesse mais a falta deste material. Foi proposta e implementada uma avaliação do desgaste do selo mecânico no plano de inspeção mensal dos equipamentos, para realizar o acompanhamento de vida útil da peça e assim identificar o momento ideal para a troca da mesma, reduzindo a possibilidade de falha por desgaste. O segundo ponto de análise, foi a indisponibilidade relacionada a alta vibração do motor de acionamento do sistema, no qual foi identificado que a principal causa era o desgaste nas tampas e rolamentos do motor de acionamento dos equipamentos. Durante a análise do histórico de falhas do equipamento foi verificado que a vibração do conjunto não era acompanhada de forma sistemática e assim causou fissura por fadiga em tubulações de condução de fluido refrigerante, danos em pista interna e elemento rolante e gaiola dos rolamentos do compressor, e desajuste do slide válvula do compressor (peça que controla a entrada de fluido refrigerante no compressor e que possui ajuste mecânico). Segundo Rao (2008), a vibração de um sistema mecânico intensifica desgaste de peças móveis, e pode ter efeitos catastróficos quando a vibração imposta ao sistema induzir ressonância ao se aproximar de uma frequência natural, gerando falhas estruturais e de componentes como rolamentos e engrenagens. O desgaste em rolamentos e tampas de motores é inerente ao seu funcionamento, mas o mesmo pode ser reduzido com uma sistemática de lubrificação, já existente para o sistema, e acompanhado por meio da realização de analises dos índices de vibração. Em ocorrências de aumento de vibração da estrutura dos chillers, foi identificado posteriormente que a mesma era causada por falhas de gaiola dos rolamentos traseiros do motor de acionamento, que causava aumento da vibração na estrutura do chiller, pois era muito próxima da frequência natural da estrutura do equipamento, e assim, o ponto causador da vibração pôde ser mais facilmente identificado. Desta forma, foram implementadas duas ações para reduzir os índices de indisponibilidade relacionados a esta causa: realização de análise de vibração espectral mensal 9 nos rolamentos dos chillers, tanto nos motores quanto nos compressores, e realização de análise de vibração global estrutural bimestralmente. Por fim, foi estudada a indisponibilidade relacionada ao fim da vida útil das gaxetas dos trocadores de calor. O histórico dos equipamentos evidencia que a causa das falhas nos trocadores de calor foi devido à montagem incorreta ou ao aperto excessivo. Dessa forma, foi constatado que nenhuma gaxeta falhou nestes equipamentos por problemas relacionados ao material. Foi então implantado um procedimento para realizar a troca destas peças, evitando assim montagens incorretas, no qual é também exigido o uso de torquimetro para realizar o aperto do trocador de calor dirimindo as falhas por aperto excessivo. Por não haver histórico de rompimento desta peça e devido à mesma ser a indicada pelo fabricante, foi avaliada a periodicidade de troca desta peça nos manuais do equipamento, e constatado que havia uma divergência entre este período de troca. Nos planos de manutenção preventiva vigentes, era realizada a troca de forma quinquenal. No entanto a troca é indicada pelo fabricante a cada dez anos. Utilizando-se a indicação do fabricante, haverá um aumento do tempo de uso da gaxeta e assim um espaçamento entre as manutenções onde haverá diminuição do tempo de indisponibilidade do equipamento para a troca das gaxetas, mas diluirá a indisponibilidade em um maior espaço de tempo.
Gráfico 3 – Relação de tempo de indisponibilidade e quantidade de defeitos/falhas detectados no sistema.

Os resultados ligados à indisponibilidade dos equipamentos foram analisados em comparação com os dados históricos disponíveis, onde pode ser notado que houve uma redução significativa do tempo de indisponibilidade dos equipamentos. Conforme Gráfico 3 houve um aumento de aproximadamente 80% do tempo de disponibilidade dos equipamentos de 2016 para 2017. Um ponto de destaque é que nos meses de setembro e outubro de 2017 não houve nenhuma ocorrência que deixasse equipamentos indisponíveis no sistema. Enquanto, no mesmo período de 2016, os equipamentos tiveram 1190 horas de indisponibilidade, ou seja, quase 10% de toda a indisponibilidade do sistema no ano de 2016, o que seria equivalente a 43% de toda a indisponibilidade do ano de 2017. Análise dos planos de manutenção A avaliação dos planos de manutenção foi incentivada por uma entrevista feita com os colaboradores que trabalham com os equipamentos, em que os mesmos relataram uma grande recorrência de paradas dos equipamentos para preventivas em curtos espaços de tempo e que havia muitas atividades repetidas e que não eram aplicáveis para o sistema. Para entender a procedência das informações relatadas pelos operadores, foi realizada uma avaliação de aplicabilidade das atividades dos planos de manutenção, comparando as atividades e suas periodicidades ao histórico disponível no sistema SAP e às orientações que o fabricante do equipamento disponibiliza no manual de operação e manutenção do equipamento. Durante a avaliação, foi detectada a realização de mais intervenções que o necessário em um determinado espaço de tempo, causado por atividades parametrizadas para acontecerem com a mesma periodicidade sendo executadas em intervalos diferentes. Ocorriam duas vezes por mês atividades cuja frequência deveria ser mensal, e cinco vezes por ano atividades cuja periodicidade deveria ser anual, como é exposto pelo Gráfico 4. Outro ponto notado foi que as atividades de diferentes periodicidades que ocorriam no mesmo mês dificilmente eram executadas em uma única intervenção no equipamento, devido à disposição das manutenções dentro do planejamento criado pelo sistema.
Gráfico 4 – Quantidade de planos relacionada com a periodicidade dos mesmos.
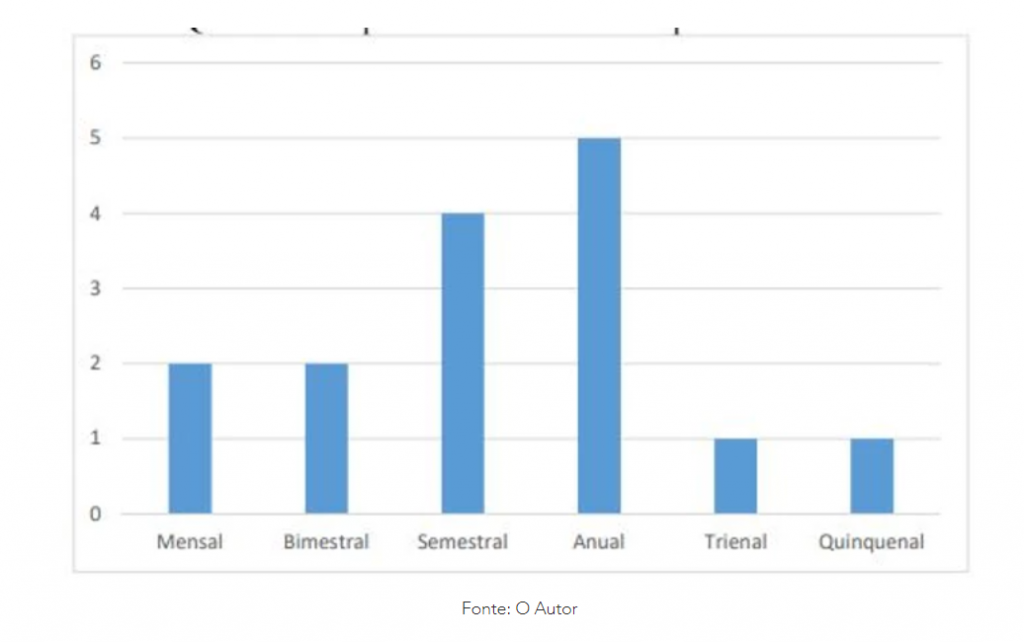
Assim foi definido que seria realizada a avaliação dos planos de manutenção observando as tarefas realizadas, a possibilidade de unir planos de mesma periodicidade e a redistribuição das atividades para que as atividades de periodicidade diferentes acontecessem da forma que causasse o menor número de intervenções possível. Durante esta reestruturação, foi constatada a execução da mesma atividade em diferentes periodicidades, o que onera o processo de manutenção e não agrega valor. Estas atividades eram, por exemplo: reaperto da fixação do motor na estrutura do equipamento, que estava contemplada no plano de manutenção bimestral, semestral e anual, e teste de vazamento de fluido refrigerante, que estava presente nos planos de periodicidade mensal e semestral. Estas inconsistências foram removidas e os planos foram unidos de modo a diminuir a quantidade de intervenções a serem realizadas. O Gráfico 5 exibe a disposição dos planos em suas periodicidades após as alterações. As mudanças feitas uniram atividades de mesma natureza. Observando como exemplo a periodicidade semestral, antes haviam três planos de manutenção mecânica e um de manutenção em instrumentação, após a reestruturação dos planos restaram um plano de manutenção mecânica e um de instrumentação.
Gráfico 5 – Alteração em planos para redução de intervenções.
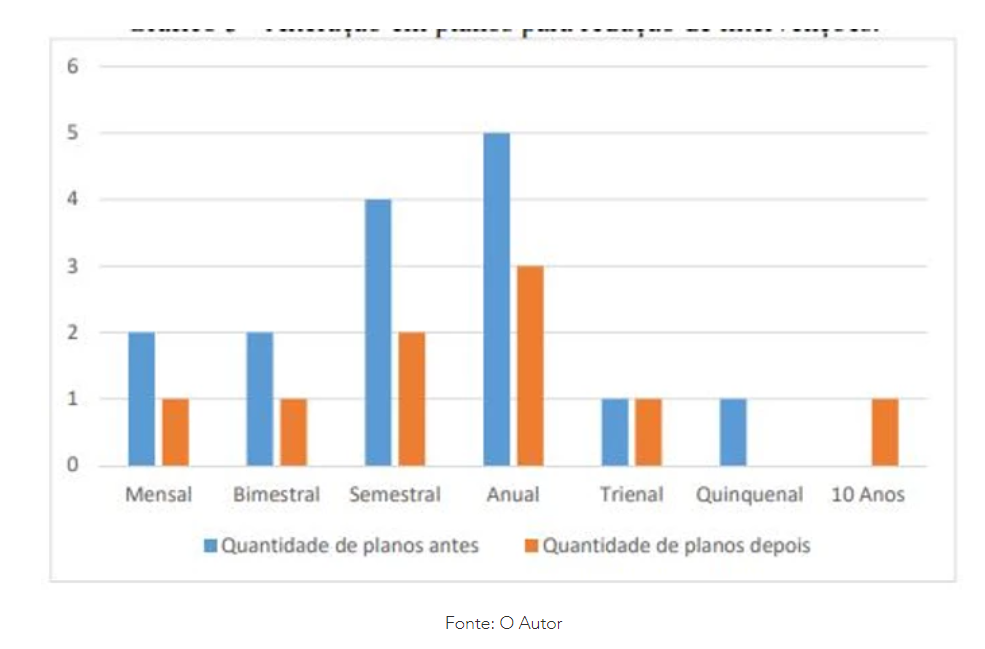
Foi realizada a redistribuição das atividades no planejamento e foi definido que as manutenções de cada equipamento aconteceriam em uma determinada semana do mês independente da periodicidade. Esta atividade pode ser melhor entendida por meio do seguinte exemplo: todas as manutenções do chiller 1 que deveriam acontecer dentro do mês seriam obrigatoriamente executadas na primeira semana do mês, reduzindo a ocorrência de intervenções desnecessárias nos equipamentos. Com estas ações implementadas foi possível realizar uma projeção da redução de intervenções no sistema, na qual foi constatado que já houve anos em que ocorreram 200 intervenções para manutenções periódicas em um ano de operação dos 4 equipamentos, e agora ocorrerão 48 intervenções anualmente no sistema. Analise de custo de peças de manutenção A análise de custos foi baseada em dados históricos e assim realizada avaliação dos maiores custos em atividades corretivas e preventivas dos chillers desde 2013. Por meio de relatórios emitidos pelo sistema ERP no qual os dados foram compilados conforme Gráfico 6.
Gráfico 6 – Pareto de custos de peças de manutenção
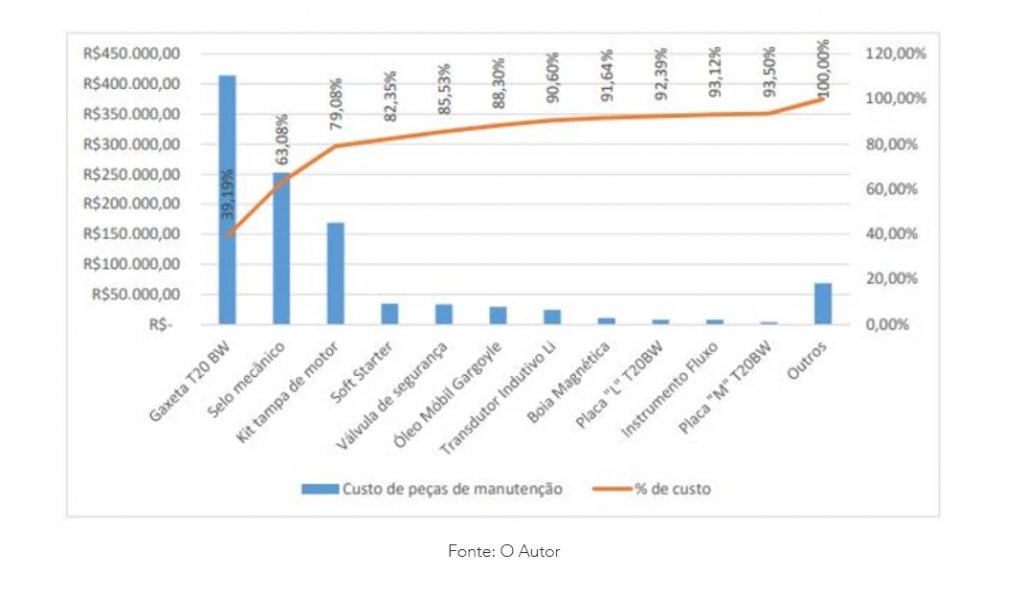
No que tange ao que é evidenciado pelo Gráfico 6 é possível notar que as peças que mais oneraram o processo de manutenção dos equipamentos foram a Gaxeta T20 BW (que é utilizada nos trocadores de calor), o selo mecânico e o Kit de tampas do motor de acionamento do chiller. O maior custo em peças para manutenção destes equipamentos é devido as gaxetas para os trocadores de calor, que é um produto nacional e comprado diretamente do fabricante. Foi identificada a oportunidade de redução de custo em uma das ações propostas para a resolução do problema de indisponibilidade. Assim com a alteração do plano de manutenção para que o mesmo atendesse a indicação do fabricante, foi alcançada uma redução de consumo desta peça e, consequentemente, a redução do custo ligada as gaxetas. Na tabela 1 pode-se notar a previsão de redução de custo com a alteração de periodicidade de troca de gaxetas nos trocadores de calor. A modificação executada em todos os 8 trocadores de calor existentes no sistema gerou uma redução de custo de R$ 300.000,00 a cada 30 anos de operação de cada equipamento, pois é necessária a execução de 50% das intervenções nos equipamentos. Assim pode-se deduzir que houve uma redução de R$ 800.000,00 a cada 10 anos de operação do sistema.
Tabela 2 – Tabela de custo de troca de gaxetas em periodicidades diferentes.
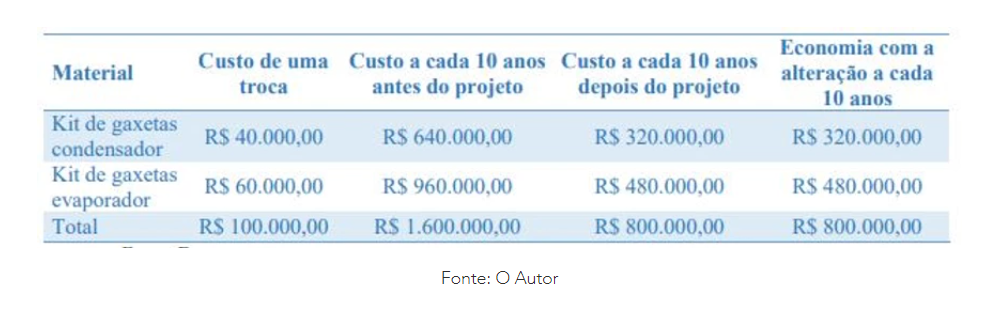
O estudo relacionado a custo de manutenção também abrangeu os selos mecânicos do chiller, peça esta que tem custo de R$ 20.155,90 quando comprada diretamente do fabricante do equipamento. Para esta peça foram levantadas duas possibilidades de redução de custo: reparo dos selos mecânicos danificados e adequação do estoque da peça. Para a opção de reparo dos selos mecânicos danificados, há um custo em torno de 13% da instalação de um selo novo. Este reparo foi cotado com duas empresas que já prestam o serviço de recuperação de selos mecânicos para a empresa. No entanto esta opção não se mostrou efetiva quando foi testada em campo, pois nenhuma das empresas conseguiu reparar o selo e obter uma durabilidade aceitável. O selo comercializado pelo fabricante tem durabilidade média de 24 meses, os selos reparados chegaram a no máximo 3 meses. A baixa durabilidade do selo é compensada pelo seu custo, mas esta opção não foi implantada devido ao retrabalho de troca do selo, operação de longa duração que aumentaria a indisponibilidade dos equipamentos, e o impacto ambiental ligado ao descarte de fluido refrigerante, necessário para a substituição do selo mecânico, como ilustrado no gráfico 7.
Gráfico 7 – Relação entre custo e durabilidade dos selos mecânicos
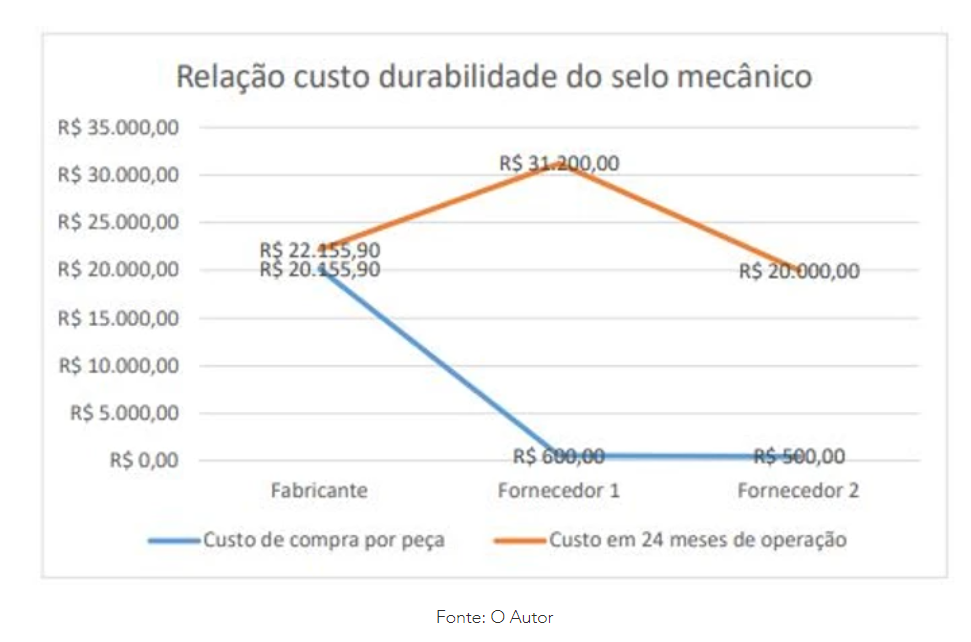
Assim, foi avaliado a adequação dos limites de estoque do selo mecânico. O estoque máximo desta peça era de uma unidade, a reposição do estoque com a compra de um selo mecânico gera o custo de aproximadamente R$ 21.000,00 devido ao custo do material somado aos débitos subsequentes (impostos e frete do material). Foi realizado o aumento de estoque para três unidades, com a compra ocorrendo sempre quando ainda houvesse uma unidade em estoque. Foi realizada a negociação e firmado um contrato para reduzir o custo de compra desta peça. A adequação do estoque gera redução do número de pedidos de compra para o mesmo material. Assim o comprador tem maior poder de negociação com o fornecedor, por fazer compras de cifras mais significativas, e uma redução de custo de frete e impostos, pois ambos são calculados com base no valor da nota fiscal. O aumento do estoque gerou uma redução de aproximadamente R$ 3.500,00 para cada selo comprado. A implantação desta melhoria trouxe como benefício principal a redução de custo de compra destas peças, e trouxe uma maior segurança para o sistema pois há mais peças disponíveis para a uma possível eventualidade, havendo quatro peças idênticas em operação somente neste sistema em estudo. Em relação ao kit de tampas dos motores elétricos que acionam o sistema, o custo de compra destas peças girava em torno de R$ 22.000,00. A compra era feita por meio de representante do fabricante do motor localizado na própria cidade o qual realizava a compra diretamente do fabricante e revendia o kit. Devido ao alto custo e baixa utilização deste material, as opções identificadas para redução do custo foi a compra direta no fabricante ou a troca do fornecedor. Ao realizar contato com o fabricante para a compra do material, o mesmo informou que, devido normas internas, não era possível a venda direto para o consumidor final e assim esta opção foi descartada. A segunda opção foi verificada com os demais representantes do fabricante do motor no estado de Minas Gerais, já que os representantes dos estados vizinhos informaram que não podiam realizar a venda por não estar em seu estado de atuação. Como pode ser visto na Tabela 2, dentro de Minas Gerais há um fornecedor que comercializa o material por um custo menor mesmo havendo o custo do frete para a cidade após a compra.
Tabela 3 – Custo de aquisição de kit de tampas para motor de acionamento dos Chillers
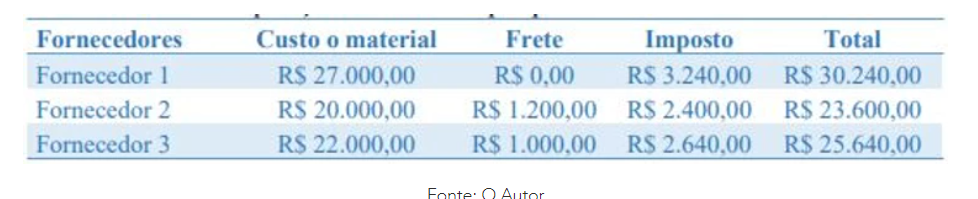
A redução de custo de manutenção para os kits de tampas teve processo muito parecido com o realizado para os selos, no entanto, como a compra é menos frequente, foi firmado contrato para garantir que nas próximas compras a redução de custo ainda se mantivesse. Assim, foi feito a padronização junto ao setor de compras para que o conjunto de tampas fosse comprado do fornecedor 2 com o preço fixado por um período de quatro anos, o que gerará uma economia, a cada kit de tampas, que necessitar ser trocada nos motores dos chillers por este período. Garantindo assim uma economia de R$ 6.640,00 a cada kit de tampas que necessitar ser trocada nos motores dos chillers durante este período. CONCLUSÃO A proposta deste trabalho foi a de aumentar a disponibilidade dos equipamentos e a redução de custo de manutenção com o foco voltado para as peças utilizadas nos mesmos. Esta proposta foi embasada em análise de dados históricos e entrevistas com operadores e técnicos de manutenção que trabalham diretamente com os equipamentos. Foram propostos planos de ação para alcançar os objetivos traçados, no qual foram implantadas melhorias em três linhas de trabalho: análise de falhas históricas em busca do aumento de disponibilidade dos equipamentos, a revisão dos planos de manutenção, e a redução de custo em peças de manutenção. Para ambos os planos de ação foram alcançados resultados substanciais que comprovaram mesmo que por previsões o resultado efetivo das ações propostas. Com o aumento de aproximadamente 80% de disponibilidade dos chillers se comparado os anos de 2016 e 2017. Outro resultado obtido com as melhorias propostas foi a redução do número de intervenções, necessárias para atividades preventivas, inspeções e preditivas, nos equipamentos por meio da revisão dos planos de manutenção. Em que foi reduzido de aproximadamente 200 para 48 intervenções por ano nos equipamentos. Esta redução, se avaliada percentualmente, pode ser considerada como uma redução de aproximadamente 76% das intervenções destes tipos que eram realizadas nos equipamentos. 17 A redução de intervenções realizadas no sistema pode ser considerada uma otimização do processo de manutenção, no qual a mão de obra que era disponibilizada para a execução do serviço otimizado pode ser aplicada em outra frente de trabalho. Por fim foram feitas projeções para avaliar as reduções de custos almejadas com as mudanças implementadas, onde pode ser previsto reduções de custo para as situações avaliadas. No qual o resultado mais considerável foi a redução 50% do custo relacionado a troca das gaxetas dos trocadores de calor dos chillers com a mudança de periodicidade de execução, onde foi alcançado uma economia de R$ 800.000,00 a cada 10 anos. Desta forma foram alcançados os objetivos traçados e o aumento da confiabilidade nos equipamentos em questão. Propomos como possíveis trabalhos futuros a investigação da ausência de tendência de ocorrências após 2014 e a aplicação de analises como as feitas nos demais sistemas de utilidades existentes na fábrica.
REFERÊNCIAS ASSOCIAÇÃO DE NORMAS TÉCNICAS.
NBR 5462-TB116: Confiabilidade e mantenabilidade. Rio de Janeiro, 1994. ALVES, André Luiz Mortari. Utilização de software de gerenciamento para manutenção no sistema de climatização dos edifícios da Câmara dos Deputados. Trabalho de Conclusão de Curso, Universidade de Brasília, 2016. FABRO, Elton et al. Modelo para planejamento de manutenção baseado em indicadores de criticidade de processo. Dissertação (Pós-graduação) – Programa de Pós-Graduação em Engenharia de Produção, Universidade Federal de Santa Catarina, Florianópolis, 2003. INCROPERA, Frank P.; DEWITT, David P.
Fundamentos de transferência de calor e de massa. 6. ed. Rio de Janeiro: LTC, 2008. KARDEC, Allan; NASCIF, Júlio. Manutenção-função estratégica. 4. ed. Rio de Janeiro: Qualitymark, 2001. RAO, Singiresu, Vibrações mecânicas, 4. ed. São Paulo: Pearson Education, 2008. TAKATA, S.; KIRNURA, F.; VAN HOUTEN, F. J. A. M.; WESTKAMPER, E.; SHPITALNI, M.; CEGLAREK, D.; LEE, J. Maintenance: Changing Role in Life Cycle Management. Annals of the CIRP, 2004. TRANE, Trane® Optimus™ Water-cooled Chillers 150 – 430 tons, 2014. Disponível em: . Acesso em: 15 out. 2017, 15:08:38 18 XENOS, Harilaus G. Gerenciando a manutenção produtiva. 2. ed. Belo Horizonte: Editora de Desenvolvimento Gerencial, 1998. YORK. Process Systems: Global Excellence in Process Refrigeration and Gas Compression Systems, 2015. Disponível em: . Acesso em: 15 out. 2017, 15:12:08 Weber Refrigeration, Heating and Air Conditioning, [Esquema de funcionamento de um Chiller] 2013, 1 ilustração. Disponível em: . Acessado em 28 out. 2017, 18:35:05
Sou a Raissa Dias, gostei muito do seu artigo tem muito
conteúdo de valor, parabéns nota 10.